
Condenser Shell and Tube: Understanding the Basics
Condenser Shell and Tube: Understanding the Basics
Condenser shell and tube is a type of heat exchanger commonly used in various industrial applications, including power plants, chemical processing plants, and refrigeration systems. The purpose of a condenser is to remove heat from a hot vapor or gas and convert it into a liquid form. The shell and tube design consists of a shell or outer chamber that houses a bundle of tubes, which are typically made of copper, brass, or stainless steel.
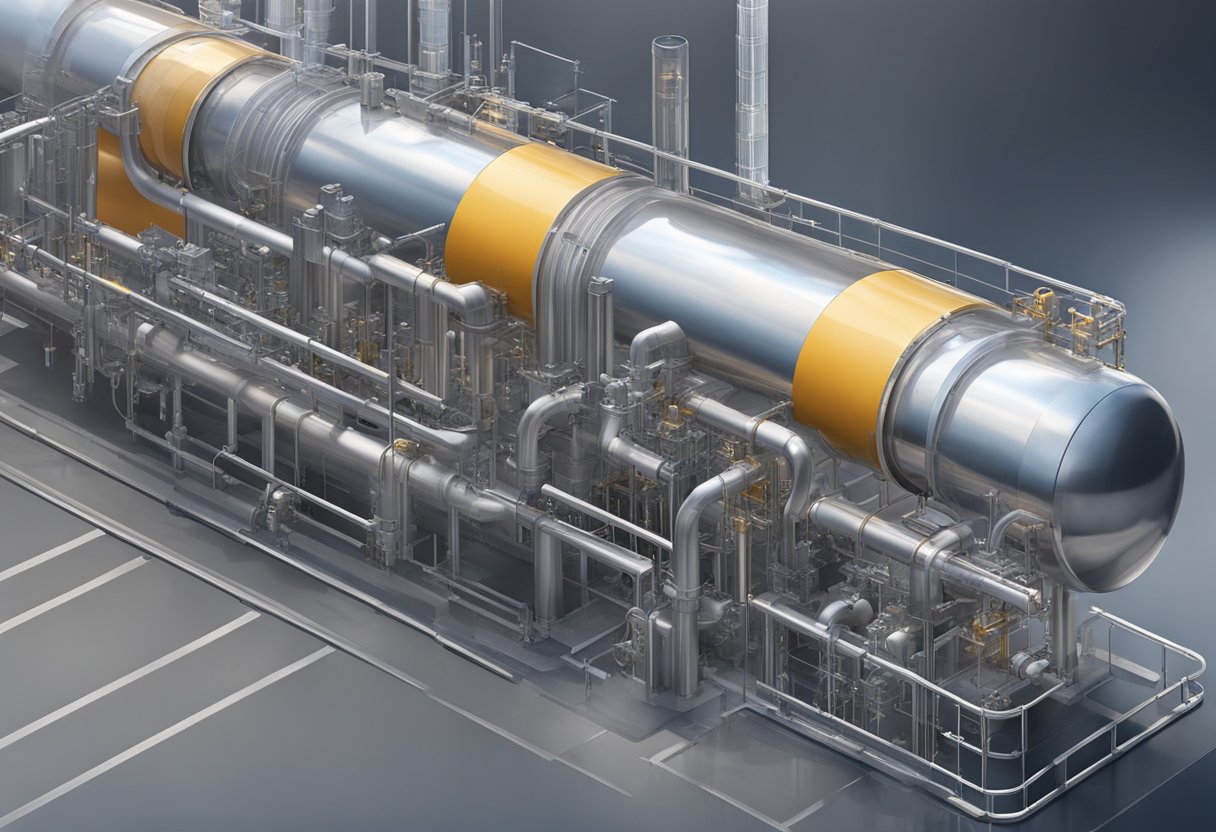
The hot vapor or gas flows through the tubes, while a cooling fluid, typically water, flows around the tubes in the shell. As the hot vapor or gas comes into contact with the cooler tubes, it releases heat energy, which is transferred to the cooling fluid. UK post code process causes the vapor or gas to condense into a liquid, which can then be collected and reused. The condenser shell and tube design is preferred in many applications because it is highly efficient and can handle a wide range of operating conditions.
Fundamentals of Shell and Tube Condensers
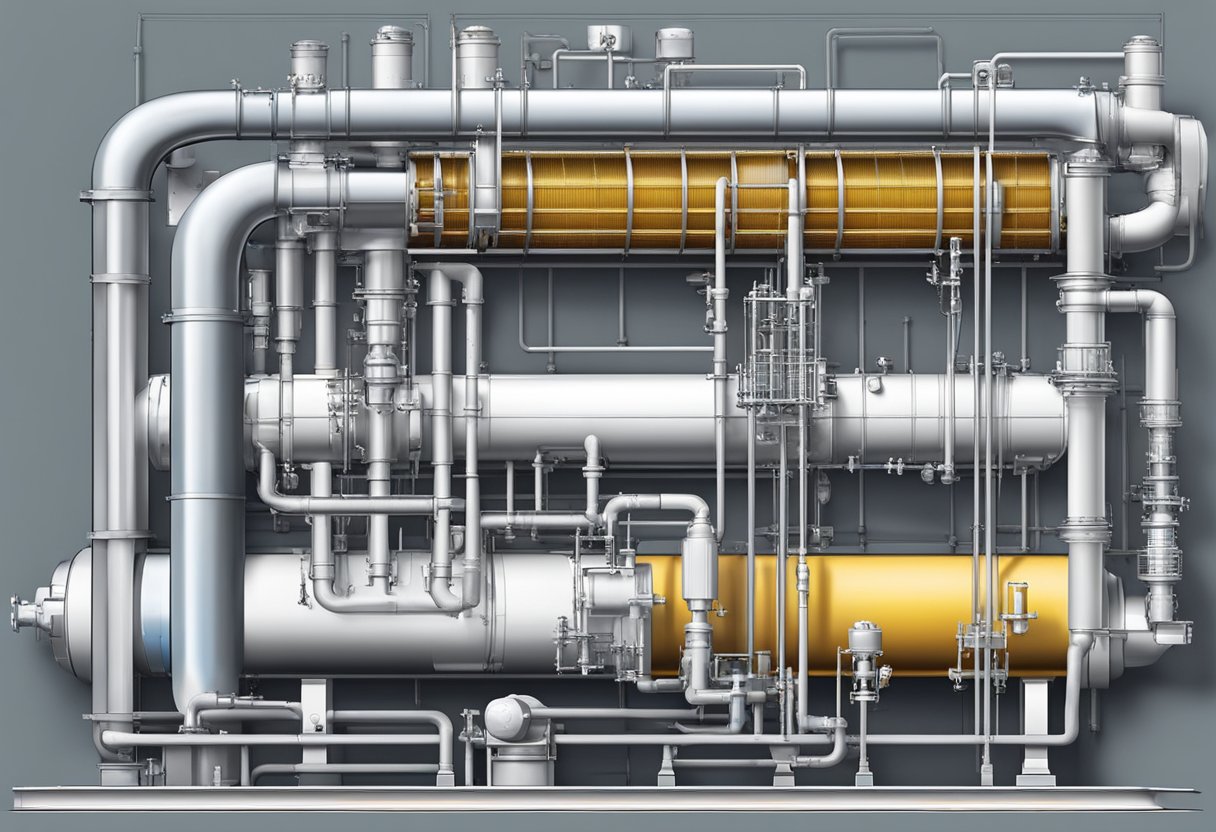
Shell and tube condensers are widely used in various industrial applications for heat transfer. They consist of a shell, which contains a bundle of tubes. The refrigerant flows through the tubes, while the cooling water flows through the shell in the opposite direction. The heat transfer occurs between the refrigerant and the cooling water through the tube walls.
One of the main advantages of shell and tube condensers is their high efficiency. They can handle Meat Bone Meal Machine large volumes of fluids and provide a large heat transfer area. This results in a high rate of heat transfer, which makes them ideal for use in applications where a large amount of heat needs to be transferred.
Another advantage of shell and tube condensers is their durability. They are constructed using high-quality materials that are resistant to corrosion and erosion. This ensures that they can withstand harsh operating conditions and have a long service life.
Shell and tube condensers are also easy to maintain. The tubes can be easily cleaned or replaced if necessary, and the shell can be opened for inspection and repair. This reduces downtime and maintenance costs, making them a cost-effective solution for many industrial applications.
In summary, shell and tube condensers are a reliable, efficient, and durable solution for heat transfer in various industrial applications. Their high efficiency, durability, and ease of maintenance make them a popular choice for many industries.
Design Specifications
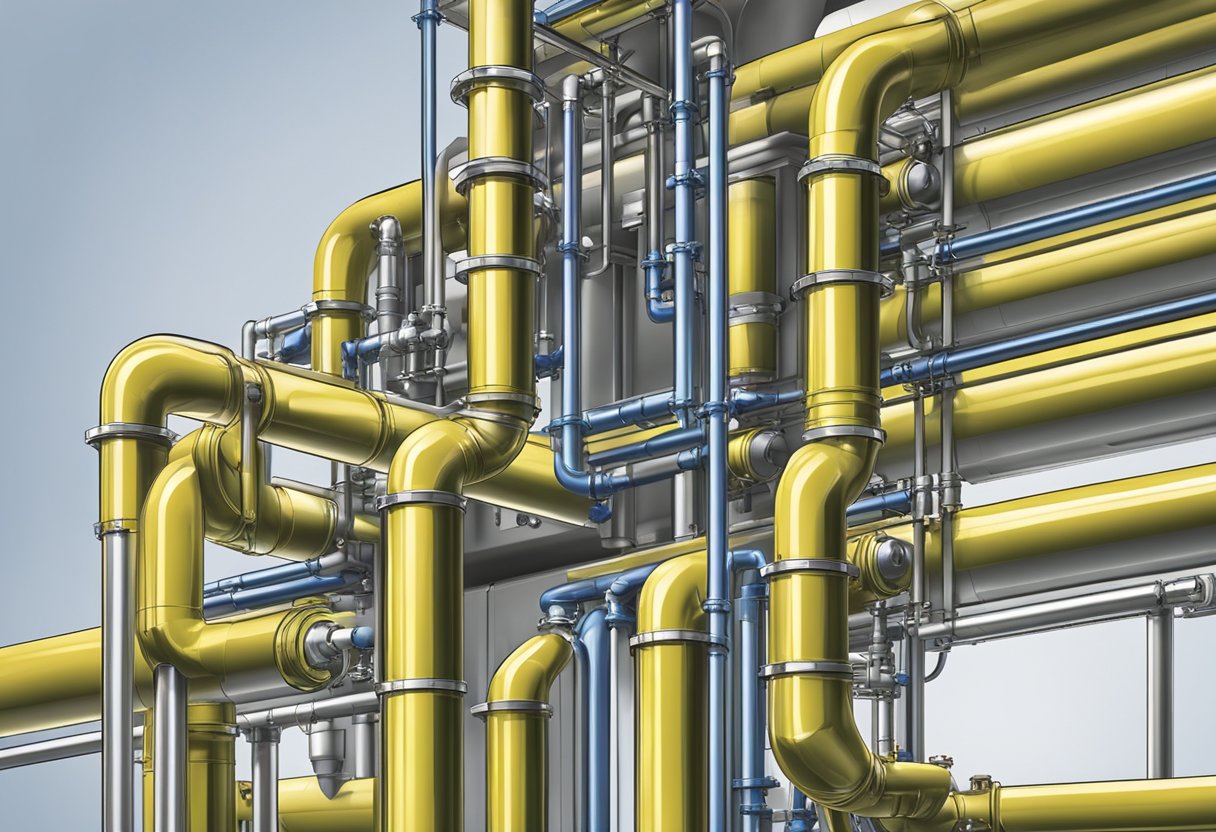
Thermal Design
The thermal design specifications for a condenser shell and tube are critical to ensure efficient heat transfer. The design must consider the fluid properties, flow rate, and temperature of both the hot and cold fluids. The heat transfer coefficient, which is a measure of how effectively heat is transferred between the fluids, should be maximized to ensure efficient operation.
To achieve optimal thermal performance, the tube material should be carefully selected based on its thermal conductivity and corrosion resistance. Additionally, the tube diameter and spacing should be chosen to facilitate adequate fluid flow and minimize pressure drop.
Mechanical Design
The mechanical design specifications for a condenser shell and tube are equally important to ensure safe and reliable operation. The design must consider factors such as the maximum allowable pressure and temperature, tube thickness, and support structure.
To prevent tube failure, the design must account for thermal expansion and contraction, which can cause stress on the tubes. Adequate support structures must be in place to prevent sagging and vibration. Additionally, the shell and tube must be designed to allow for easy maintenance and cleaning.
UK post code, the design specifications for a condenser shell and tube must balance thermal performance with mechanical reliability to ensure efficient and safe operation.
Construction Materials
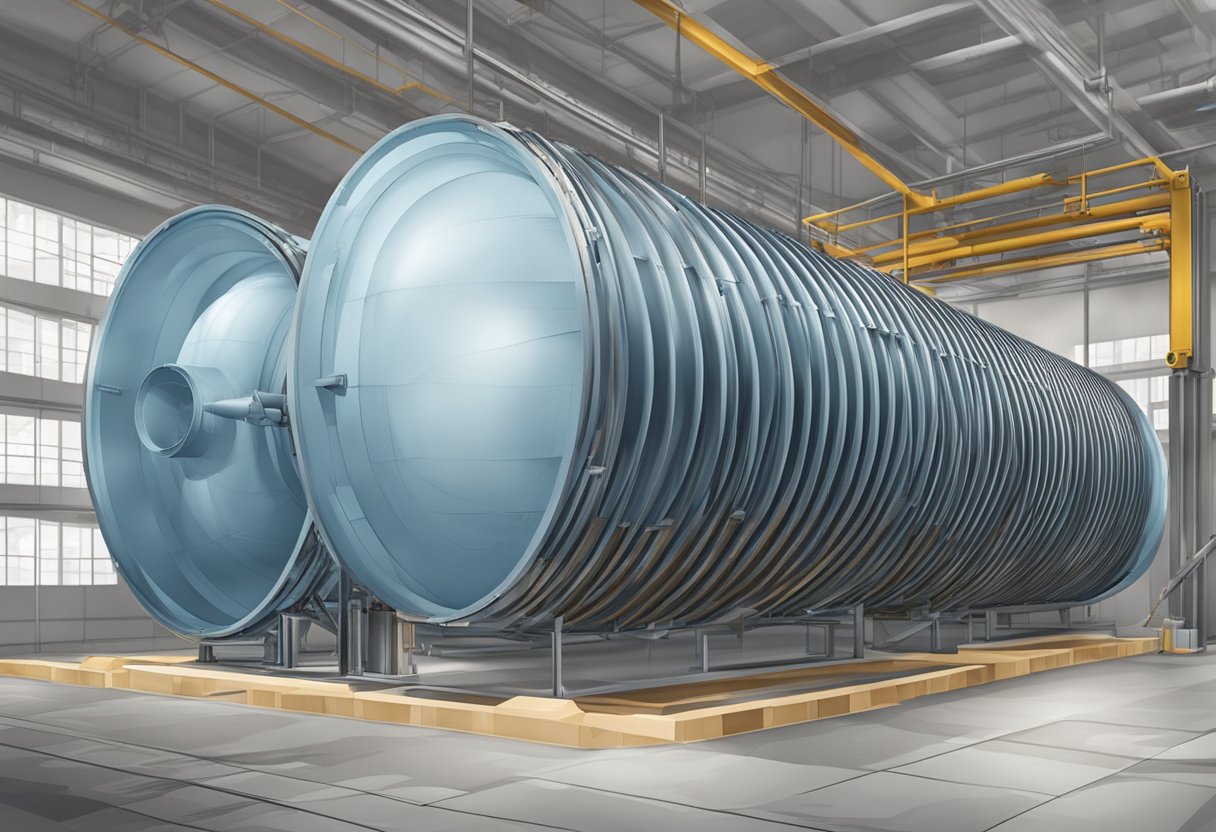
Tube Materials
The tubes in a condenser shell and tube are typically made from copper, brass, or stainless steel. Copper tubes are commonly used due to their excellent heat transfer properties and corrosion resistance. Brass tubes are also used for their corrosion resistance and are often preferred for seawater applications. Stainless steel tubes are less common but are used in applications where high temperatures or corrosive materials are present.
Shell Materials
The shell of a condenser shell and tube is typically made from carbon steel, stainless steel, or titanium. Carbon steel is the most common material used due to its strength and affordability. Stainless steel is used in applications where corrosion resistance is a concern. Titanium is a more expensive option but is preferred in applications where the condenser will be exposed to seawater or other corrosive materials.
Overall, the materials used in the construction of a condenser shell and tube are carefully selected based on the specific application and operating conditions. By selecting the appropriate materials, the condenser can operate efficiently and effectively for an extended period of time.
Heat Transfer Principles
Condensation Heat Transfer
In a shell and tube condenser, the vapor condenses on the outer surface of the tubes, releasing heat to the cooling water flowing inside the tubes. The heat transfer during condensation is a complex process that involves the transfer of latent heat and sensible heat. The latent heat transfer occurs when the vapor changes phase into a liquid, while sensible heat transfer occurs due to the temperature difference between the vapor and the cooling water.
The rate of condensation heat transfer depends on several factors, including the physical properties of the vapor and the cooling water, the geometry of the condenser, and the flow rates of the vapor and the cooling water. The heat transfer coefficient, which is a measure of the efficiency of the heat transfer process, is also influenced by these factors.
Overall Heat Transfer Coefficient
The overall heat transfer coefficient (U) is a measure of the overall efficiency of the heat transfer process in a shell and tube condenser. It takes into account the resistances to heat transfer on both the vapor and cooling water sides of the condenser. The overall heat transfer coefficient is calculated using the following equation:
U = 1 / ((1 / h_i) + (t_i / k) + (t_o / k) + (1 / h_o))
Where h_i and h_o are the heat transfer coefficients on the vapor and cooling water sides, respectively, t_i and t_o are the thicknesses of the tube and shell walls, and k is the thermal conductivity of the tube material.
In general, a higher overall heat transfer coefficient indicates a more efficient heat transfer process, which results in a smaller condenser size and lower energy consumption. Therefore, it is important to optimize the design of the condenser to achieve the highest possible overall heat transfer coefficient.
Operational Considerations
Flow Arrangements
In a condenser shell and tube, there are two main types of flow arrangements: parallel flow and counterflow. Parallel flow is when the refrigerant and cooling water both flow in the same direction, while counterflow is when they flow in opposite directions.
Parallel flow is typically used in situations where the cooling water is significantly colder than the refrigerant, as it allows for more efficient heat transfer. However, it can result in a higher pressure drop and may not be suitable for all applications.
Counterflow, on the other hand, is better suited for situations where the cooling water is only slightly cooler than the refrigerant. It results in a lower pressure drop, but may not be as efficient at transferring heat.
Pressure Drop
Pressure drop is an important consideration in the operation of a condenser shell and tube. It refers to the decrease in pressure that occurs as the refrigerant and cooling water flow through the system.
A high pressure drop can result in decreased efficiency and increased energy consumption. It can also cause damage to the system over time. Therefore, it is important to ensure that the pressure drop is kept within acceptable limits.
There are several factors that can contribute to pressure drop, including the flow rate of the refrigerant and cooling water, the diameter of the tubes, and the length of the tubes. By carefully considering these factors and designing the system accordingly, it is possible to minimize pressure drop and ensure optimal performance.
Maintenance and Cleaning
Fouling and Scaling
Fouling and scaling are common issues that can occur in condenser shell and tube systems, which can lead to reduced efficiency, increased energy costs, and potential equipment damage. Fouling refers to the accumulation of dirt, debris, and other substances on the surface of the tubes, while scaling is the buildup of mineral deposits on the tube walls.
To prevent fouling and scaling, regular maintenance and cleaning are essential. This may involve inspecting the system for signs of fouling or scaling, and implementing a cleaning schedule based on the severity of the buildup. In some cases, chemical treatments may be necessary to remove stubborn deposits.
Cleaning Techniques
There are several cleaning techniques that can be used to remove fouling and scaling from condenser shell and tube systems. These include mechanical cleaning, chemical cleaning, and high-pressure water cleaning.
Mechanical cleaning involves the use of brushes, scrapers, or other tools to physically remove fouling and scaling from the tube surface. Chemical cleaning uses a specific chemical solution to dissolve the buildup, while high-pressure water cleaning involves the use of high-pressure water jets to blast away the deposits.
It is important to note that the cleaning technique used will depend on the type and severity of the fouling or scaling. It is recommended to consult with a professional technician or manufacturer for guidance on the most appropriate cleaning method for a specific system.
Regular maintenance and cleaning of condenser shell and tube systems can help to prevent fouling and scaling, ensuring optimal performance and energy efficiency.
Performance Evaluation
Testing Methods
Performance evaluation of condenser shell and tube is crucial to ensure the efficient operation of the system. The testing methods used to evaluate the performance of the condenser shell and tube include:
- Heat transfer coefficient measurement
- Pressure drop measurement
- Fouling factor measurement
Heat transfer coefficient measurement involves determining the rate of heat transfer from the hot fluid to the cold fluid. Pressure drop measurement involves determining the pressure drop across the condenser. Fouling factor measurement involves determining the fouling resistance of the condenser.
Performance Metrics
The performance of the condenser shell and tube can be evaluated using various performance metrics, including:
- Overall heat transfer coefficient (U)
- Heat transfer rate (Q)
- Effectiveness (ε)
- Coefficient of performance (COP)
The overall heat transfer coefficient (U) is a measure of the overall heat transfer rate between the hot and cold fluids. The heat transfer rate (Q) is a measure of the amount of heat transferred between the hot and cold fluids. The effectiveness (ε) is a measure of the ratio of the actual heat transfer rate to the maximum possible heat transfer rate. The coefficient of performance (COP) is a measure of the efficiency of the system.
In conclusion, the performance evaluation of condenser shell and tube is essential to ensure the efficient operation of the system. The testing methods and performance metrics used to evaluate the performance of the condenser shell and tube can help identify any issues and optimize the system’s performance.
Safety and Standards
Safety Precautions
When working with condenser shell and tube, it is important to take proper safety precautions. This includes wearing appropriate personal protective equipment such as gloves, safety glasses, and hearing protection. Additionally, workers should be trained on how to safely handle and operate the equipment.
One of the biggest safety concerns when working with condenser shell and tube is the risk of exposure to hazardous materials such as refrigerants. Workers should be trained on how to properly handle and dispose of these materials to minimize the risk of exposure.
Industry Standards
The use of condenser shell and tube is regulated by industry standards to ensure that equipment is manufactured and installed safely. One of the most widely recognized standards is the American Society of Mechanical Engineers (ASME) Boiler and Pressure Vessel Code. This code outlines the requirements for the design, fabrication, and inspection of pressure vessels, including condenser shell and tube.
In addition to the ASME code, there are other industry standards that may apply depending on the specific application and location of the equipment. For example, the Environmental Protection Agency (EPA) has regulations in place to govern the use of refrigerants, which may impact the design and operation of condenser shell and tube.
By adhering to these industry standards, manufacturers and operators can ensure that their equipment is safe and reliable.