
Rosca Transportadora: The Efficient and Reliable Way to Move Materials
Rosca Transportadora: The Efficient and Reliable Way to Move Materials
A “rosca transportadora” is a type of conveyor that is commonly used in industrial settings to move materials from one location to another. This type of conveyor is designed to be highly efficient and reliable, making it an essential piece of equipment in many manufacturing and processing plants.
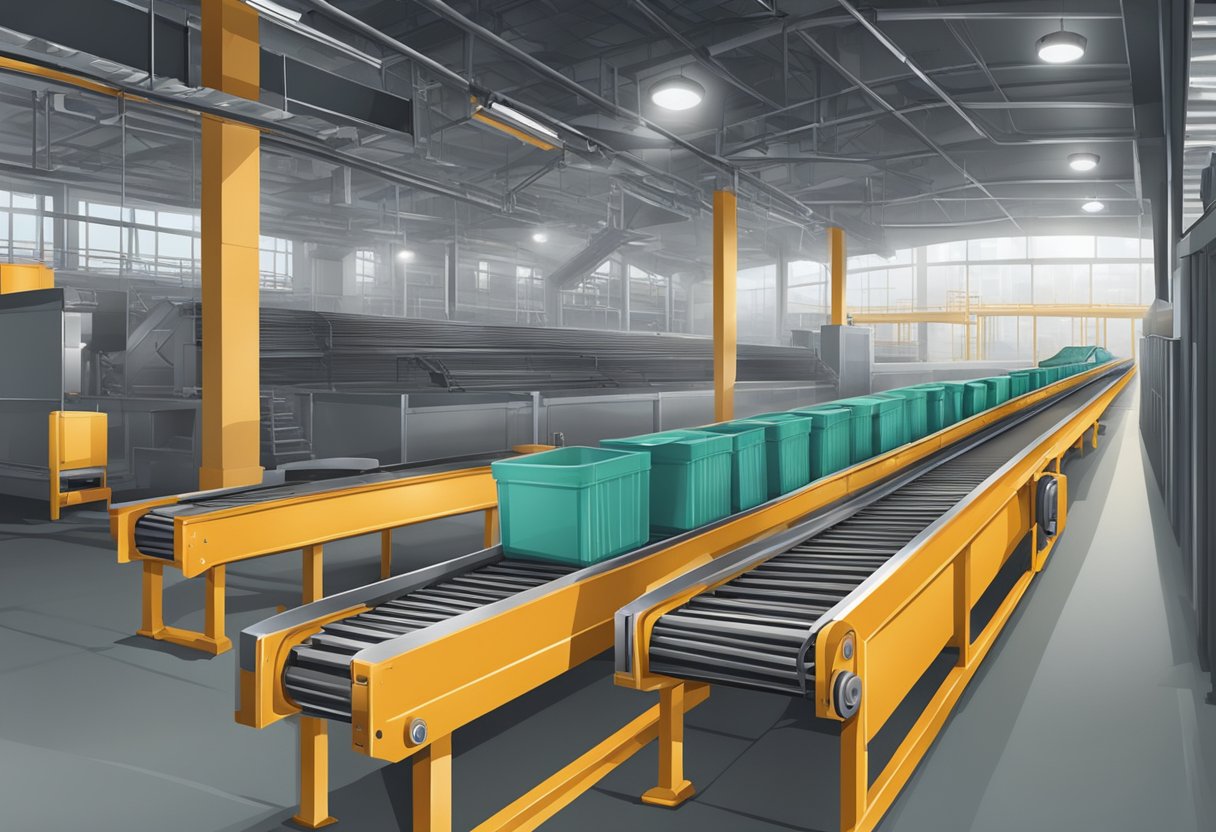
One of the key advantages of a “rosca transportadora” is its ability to handle a wide range of materials, including powders, granules, and other small particles. This versatility makes it a popular choice for many different industries, from food processing and pharmaceuticals to mining and construction.
Another important feature of a “rosca transportadora” is its ability to move materials quickly and efficiently, which can help to reduce production times and improve overall productivity. With its simple design and easy-to-use controls, this type of conveyor is an excellent choice for companies looking to streamline their operations and improve their bottom line.
Design and Functionality

Components of a Screw Conveyor
A screw conveyor, also known as a rosca transportadora, is a mechanism used to move materials in a horizontal or inclined plane. The basic components of a screw conveyor include a screw blade, a trough, a drive unit, and an inlet and discharge chute.
The screw blade is the main component that moves the material along the trough. It can be designed in different shapes and configurations to suit the specific material being transported. The trough is the channel that holds the material and guides it along the length of the conveyor. The drive unit provides the power to rotate the screw blade, which in turn moves the material. The inlet and discharge chutes are used to load and unload the material from the conveyor.
Types of Screw Conveyors
There are several types of screw conveyors available, each designed for specific applications. The most common types include horizontal screw conveyors, inclined screw conveyors, and vertical screw conveyors.
Horizontal screw conveyors are used for moving materials horizontally, typically over short distances. Inclined screw conveyors are used for moving materials at an inclined angle, usually between 10 and 60 degrees. Vertical screw conveyors are used for moving materials vertically, typically between floors or levels.
Operating Principle
The operating principle of a screw conveyor is simple. The material is fed into the inlet chute and moves along the trough as the screw blade rotates. As the material moves along the trough, it is pushed forward by the screw blade. The rotation of the screw blade creates a continuous flow of material, which is discharged through the outlet chute.
Screw conveyors are widely used in various industries, including agriculture, food processing, mining, and construction. They are known for their simplicity, reliability, and flexibility, making them an ideal choice for many material handling applications.
Applications and Industries

Agriculture
Rosca transportadora is widely used in the agriculture industry for the transportation of various agricultural products such as grains, seeds, and fertilizers. The screw conveyor’s ability to handle different types of materials makes it an ideal option for farmers and agricultural companies. Moreover, the conveyor’s design allows for easy and efficient transport of materials even in harsh environments.
Food Processing
In the food processing industry, screw conveyors are used for transporting raw materials such as grains, sugar, and flour, as well as finished products such as snacks, cereals, and pet food. The conveyor’s enclosed design prevents contamination and ensures that the products remain safe and hygienic. Additionally, the conveyor’s gentle handling of materials helps to maintain the integrity of the products.
Pharmaceuticals
The pharmaceutical industry requires the transportation of various materials such as powders, tablets, and capsules. Rosca transportadora is an ideal solution for this industry as it can handle delicate materials without causing damage. Moreover, the conveyor’s enclosed design prevents contamination and ensures that the materials remain safe and hygienic.
Mining
In the mining industry, screw conveyors are used for the transportation of various materials such as coal, ores, and minerals. The conveyor’s ability to handle large volumes of materials makes it an ideal option for mining companies. Additionally, the conveyor’s design allows for easy and efficient transport of materials even in harsh and rugged environments.
Overall, rosca transportadora is a versatile and efficient solution for various industries and applications. Its ability to handle different types of materials, gentle handling of products, and enclosed design make it a popular choice for many companies.
Material Handling Capabilities

Bulk Material Types
Rosca transportadora is capable of handling a wide range of bulk materials, including powders, granules, pellets, and flakes. Some common materials that can be transported with a rosca transportadora include sugar, salt, flour, cement, sand, and plastic pellets. The conveyor can also handle abrasive and corrosive materials, as well as materials with high temperatures.
Capacity and Flow Rates
The capacity and flow rates of the rosca transportadora can vary depending on the size and configuration of the conveyor. However, most conveyors are designed to handle a high volume of material at a consistent rate. The conveyor can be used for both continuous and batch processing, making it a versatile option for many industries.
Incline and Decline Conveying
The rosca transportadora can be designed to handle incline and decline conveying, allowing for materials to be transported up or down an incline. This feature is particularly useful for applications where space is limited or where materials need to be transported to different levels in a facility. The conveyor can also be designed to handle curves and turns, further increasing its flexibility and versatility.
Overall, the rosca transportadora is a reliable and efficient material handling solution that can be customized to meet the specific needs of a wide range of industries. With its ability to handle a variety of bulk materials, high capacity and flow rates, and incline and decline conveying capabilities, the rosca transportadora is a valuable addition to any manufacturing or processing facility.
Safety and Compliance
Safety Features
Rosca transportadora is designed with several safety features to ensure the safety of both the operators and the products being transported. The following are some of the safety features of Rosca transportadora:
- Emergency Stop Button: The emergency stop button is located at strategic points on the machine and can be easily accessed by the operator in case of an emergency.
- Safety Guards: The machine is fitted with safety guards to prevent operators from coming into contact with moving parts of the machine.
- Sensors: The machine is equipped with sensors that detect any anomalies during operation and immediately stop the machine to prevent accidents.
Regulatory Standards
Rosca transportadora is designed to meet all regulatory standards set by the relevant authorities. The machine is designed to comply with the following standards:
- CE Marking: Rosca transportadora is CE marked, which means it meets all the safety, health, and environmental protection requirements set by the European Union.
- OSHA: The Occupational Safety and Health Administration (OSHA) is a federal agency that ensures workplace safety in the United States. Rosca transportadora is designed to comply with all OSHA regulations.
- ISO 9001: Rosca transportadora is designed to comply with the ISO 9001 standard for quality management systems.
In conclusion, Rosca transportadora is designed with safety and compliance in mind. The machine is fitted with several safety features to ensure the safety of both the operators and the products being transported. It is also designed to meet all regulatory standards set by the relevant authorities.
Installation and Maintenance
Installation Guidelines
Before installing a rosca transportadora, it is important to ensure that the area where it will be installed is clean and free of any debris or obstructions. The installation process should be carried out by a qualified technician who has experience in working with conveyor systems.
During installation, it is important to follow the manufacturer’s instructions carefully. This includes ensuring that all components are securely fastened and that the conveyor is level and properly aligned. Any deviations from the manufacturer’s instructions could result in damage to the conveyor or cause it to malfunction.
Maintenance Procedures
Regular maintenance is essential to ensure the smooth operation of a rosca transportadora. This includes inspecting the conveyor for any signs of wear and tear, such as frayed belts or damaged rollers. Any damaged components should be replaced immediately to prevent further damage to the conveyor.
It is also important to keep the conveyor clean and free of debris. This can be done by regularly removing any buildup of dust or other materials that may accumulate on the conveyor. Additionally, lubricating the moving parts of the conveyor can help to prevent wear and tear and prolong its lifespan.
Troubleshooting
If the rosca transportadora is not functioning properly, it is important to identify the cause of the problem as soon as possible. This may involve checking for any loose or damaged components, such as belts or rollers. If the problem cannot be identified or resolved, it may be necessary to contact a qualified technician for assistance.
In addition to regular maintenance, it is also important to carry out any necessary repairs promptly to prevent further damage to the conveyor. This can help to minimize downtime and ensure that the conveyor is running smoothly and efficiently.
Advancements in Technology
Automation and Control Systems
Rosca transportadora has come a long way since its inception. One of the most significant advancements in technology has been the development of automation and control systems. These systems have revolutionized the way in which rosca transportadora operates. With the use of automation and control systems, the entire process of conveying materials has become more efficient and reliable.
Automation and control systems have made it possible to monitor the entire process of rosca transportadora, from the moment the material is loaded onto the conveyor to the moment it is offloaded. These systems use sensors and other monitoring devices to ensure that the material is being conveyed at the right speed and in the right direction. They also allow for real-time adjustments to be made to the conveyor system, ensuring that any issues are addressed immediately.
Material Innovations
Another area of advancement in rosca transportadora technology has been in the development of new materials. These materials have been designed to withstand the harsh conditions of the conveyor system, ensuring that they last longer and require less maintenance.
One such material is polyurethane. Polyurethane is a highly durable material that is resistant to abrasion, chemicals, and heat. It is also resistant to water and oil, making it an ideal material for use in rosca transportadora. Polyurethane is also flexible, which means that it can be molded into a variety of shapes and sizes, making it ideal for use in conveyor belts.
Another material innovation is the use of carbon fiber. Carbon fiber is a lightweight and strong material that is ideal for use in rosca transportadora. It is resistant to heat and abrasion, making it ideal for use in high-temperature environments. Carbon fiber is also resistant to chemicals, which means that it can withstand exposure to harsh chemicals without deteriorating.
In conclusion, the advancements in technology have had a significant impact on the way rosca transportadora operates. Automation and control systems have made the process more efficient and reliable, while material innovations have made the conveyor system more durable and long-lasting. These advancements are set to continue, making rosca transportadora an even more essential part of the manufacturing process.
Selection and Customization
Choosing the Right Conveyor
When selecting a rosca transportadora, it is important to consider the specific needs of the application. Factors such as the type of material being transported, the distance it needs to travel, and the desired speed and capacity should all be taken into account.
One key consideration is the type of conveyor belt needed. Different materials and designs are available, including flat belts, modular plastic belts, and wire mesh belts. The choice will depend on factors such as the weight and shape of the material, as well as the desired level of grip and friction.
Other features to consider include the size and shape of the conveyor, as well as the type of drive mechanism. Some conveyors are powered by electric motors, while others use pneumatic or hydraulic systems. The choice will depend on factors such as the available power source and the desired level of control.
Customization Options
Rosca transportadoras can be customized to meet the specific needs of a wide range of applications. Some common customization options include:
- Adjustable speed settings: Many conveyors can be adjusted to run at different speeds, allowing for greater flexibility and control.
- Variable width and length: Conveyors can be designed to accommodate different material sizes and shapes, with adjustable width and length settings.
- Customized belt materials: Depending on the specific needs of the application, different belt materials can be used, including FDA-approved materials for food handling and processing.
- Additional features: Many conveyors can be equipped with additional features such as sensors, alarms, and safety guards, to ensure safe and efficient operation.
By carefully selecting and customizing a rosca transportadora, businesses can ensure that they have the right equipment for their specific needs, improving efficiency and reducing downtime.
Categories
Recent Posts
-
What is harmless treatment of sick and dead animals and poultry(rendering plant) A Key Initiative to Protect the Ecological Environment and Food Safety.
March 6, 2025 -
How does Sunrise rendering plant equipment destroy avian influenza viruses in livestock poultry carcasses
March 5, 2025 -
Sunrise Rendering Thailand Exhibition
March 5, 2025