
Secador Rotatorio: A Comprehensive Guide to Rotary Dryers
Secador Rotatorio: A Comprehensive Guide to Rotary Dryers
A secador rotatorio, also known as a rotary dryer, is a type of industrial dryer that is commonly used for the drying of materials in a wide range of industries. These dryers are designed to work by tumbling materials in a rotating drum while a stream of hot gas is passed through the drum. The hot gas dries the materials as they tumble, resulting in a more efficient and effective drying process.
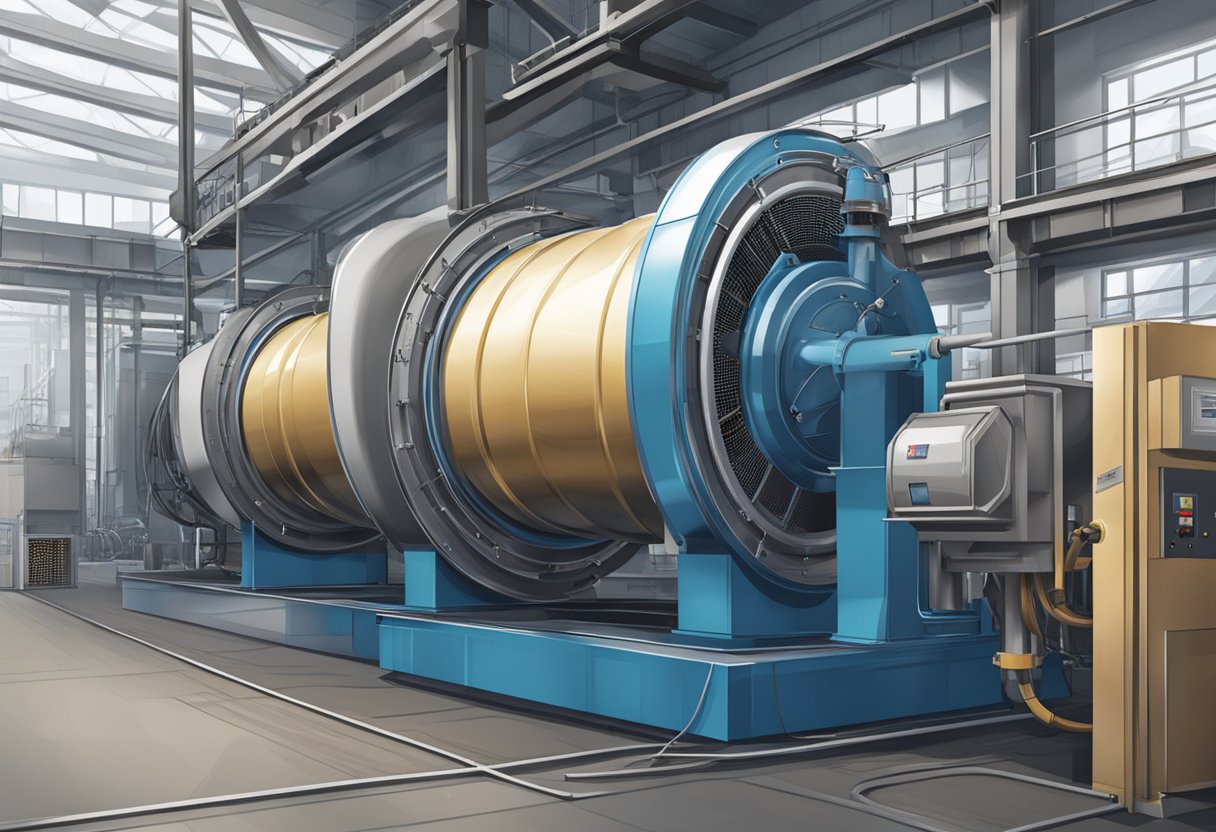
Secador rotatorios are used in a variety of applications, including the drying of minerals, agricultural products, and industrial waste. They are particularly useful for drying materials that are difficult to dry using other methods, such as those that are sticky or have a high moisture content. The design of the rotary dryer allows for a high level of control over the drying process, with the ability to adjust the temperature, airflow, and other parameters to achieve the desired level of drying.
Fundamentals of Rotary Dryers
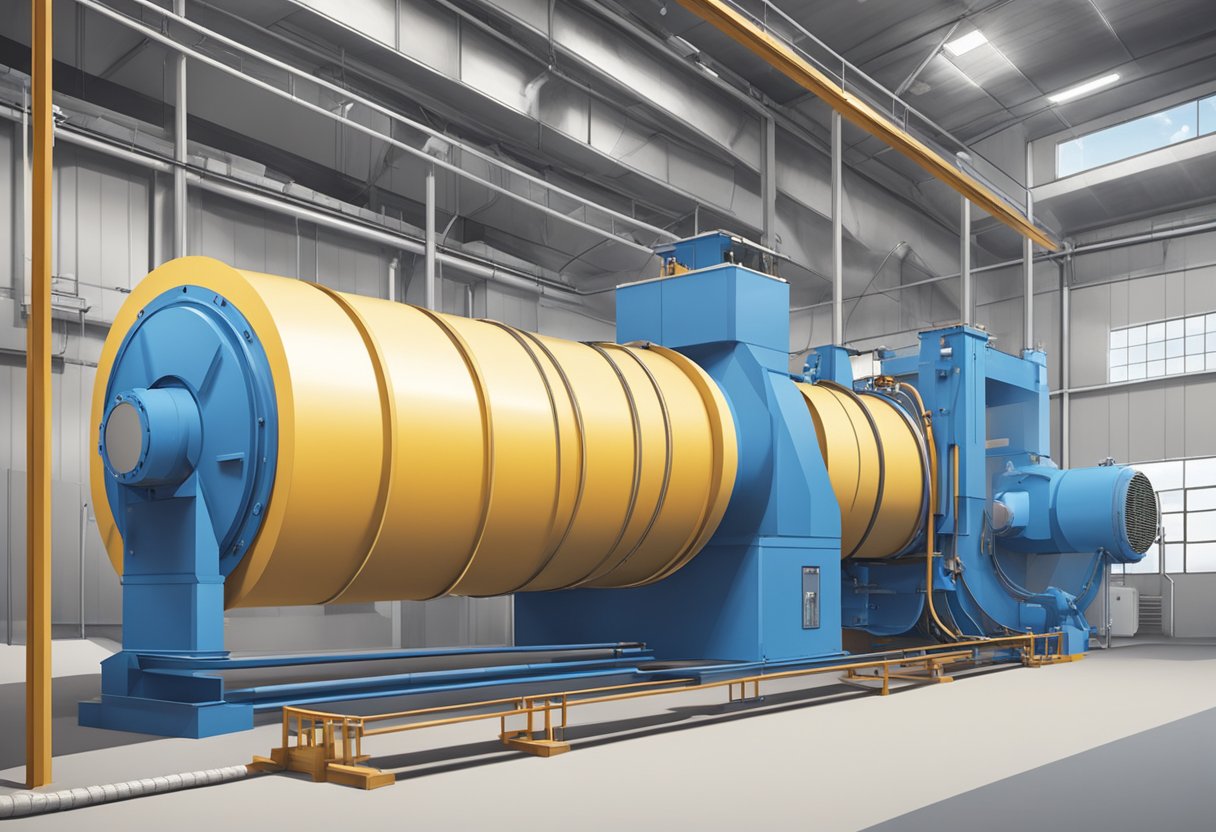
Operating Principles
Rotary dryers are a common type of industrial dryer that are used to remove moisture from a material. The basic operating principle of a rotary dryer is simple: heat and mass transfer occur between the material and the drying medium to remove moisture. The material is fed into the rotating drum, which is heated by the drying medium. As the drum rotates, the material is lifted up and dropped back down, allowing it to come into contact with the hot drying medium and release moisture. The moisture is then removed from the dryer through an exhaust system.
Design Features
Rotary dryers are designed with several key features to ensure efficient and effective drying. One important design feature is the flight design. Flights are the curved plates that are attached to the interior of the drum and help to lift and drop the material. The flight design can be customized to achieve the desired drying rate and to prevent material buildup.
Another important design feature is the sealing system. Rotary dryers must be tightly sealed to prevent air leaks, which can reduce the efficiency of the drying process. The sealing system can be designed to accommodate different types of materials and operating conditions.
In addition to flight design and sealing systems, rotary dryers can also be equipped with various types of heat sources, including gas, oil, or electric heating. The choice of heat source will depend on the specific needs of the application and the availability of the required energy source.
Overall, rotary dryers are a reliable and efficient option for removing moisture from a wide range of materials. With the right design features and operating principles, rotary dryers can be customized to meet the needs of any application.
Types of Rotary Dryers
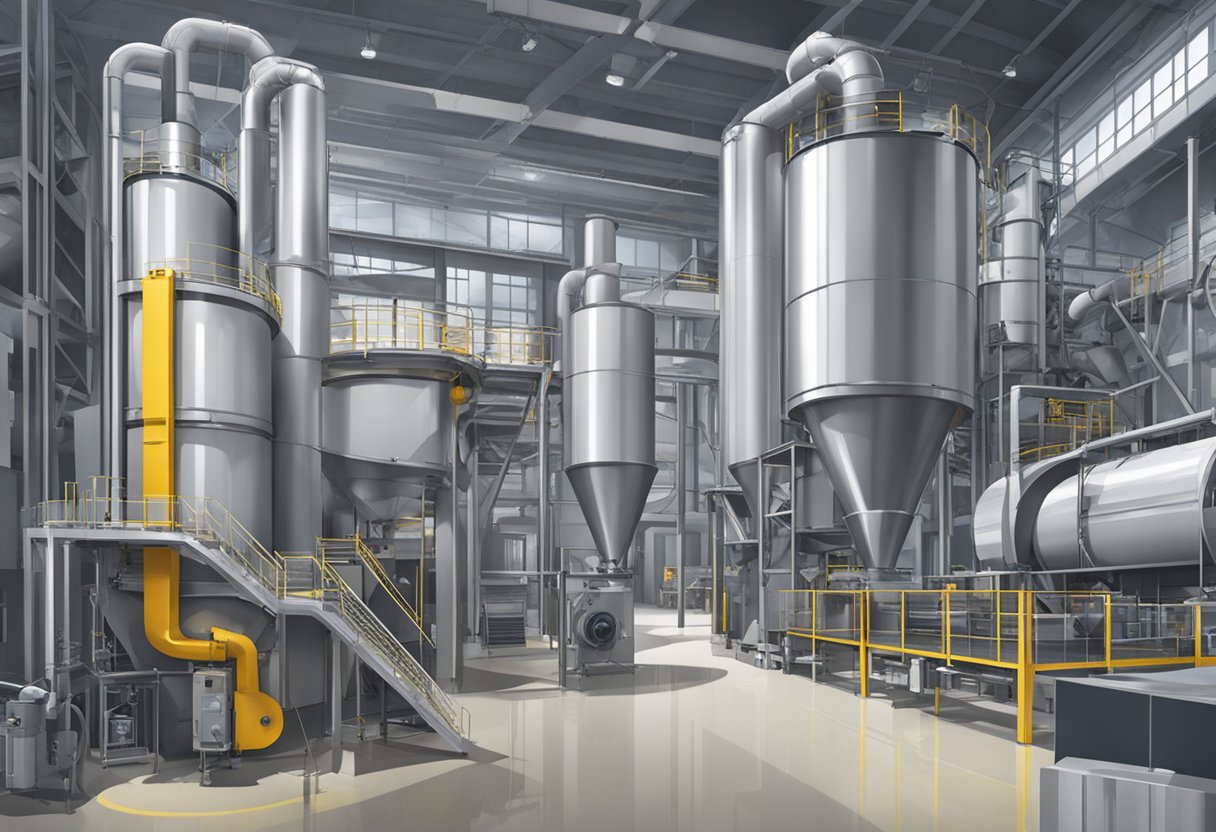
Rotary dryers are used in various industries for drying different materials. There are two main types of rotary dryers: direct heated and indirect heated. Both types have their own advantages and disadvantages.
Direct Heated Rotary Dryers
Direct heated rotary dryers are the most common type of rotary dryer. In this type of dryer, a direct flame or hot gas is used to heat the material being dried. The material comes in direct contact with the hot gas, which provides heat transfer.
Direct heated rotary dryers are efficient and can handle a wide variety of materials, including powders, granules, and even sticky materials. They are also relatively simple to operate and maintain.
However, direct heated rotary dryers can produce a lot of dust and can be difficult to control the temperature. They can also be limited in the amount of material they can handle at one time.
Indirect Heated Rotary Dryers
Indirect heated rotary dryers use hot gas or steam to heat the material being dried. The hot gas or steam does not come in direct contact with the material, but instead heats a separate chamber that contains the material.
Indirect heated rotary dryers are ideal for materials that are sensitive to direct contact with hot gas or steam. They are also more energy-efficient than direct heated rotary dryers because the hot gas or steam can be recycled.
However, indirect heated rotary dryers are more complicated to operate and maintain than direct heated rotary dryers. They also require a separate chamber for heating the material, which can add to the overall cost of the dryer.
Overall, the type of rotary dryer chosen will depend on the specific material being dried and the requirements of the industry.
Components and Specifications
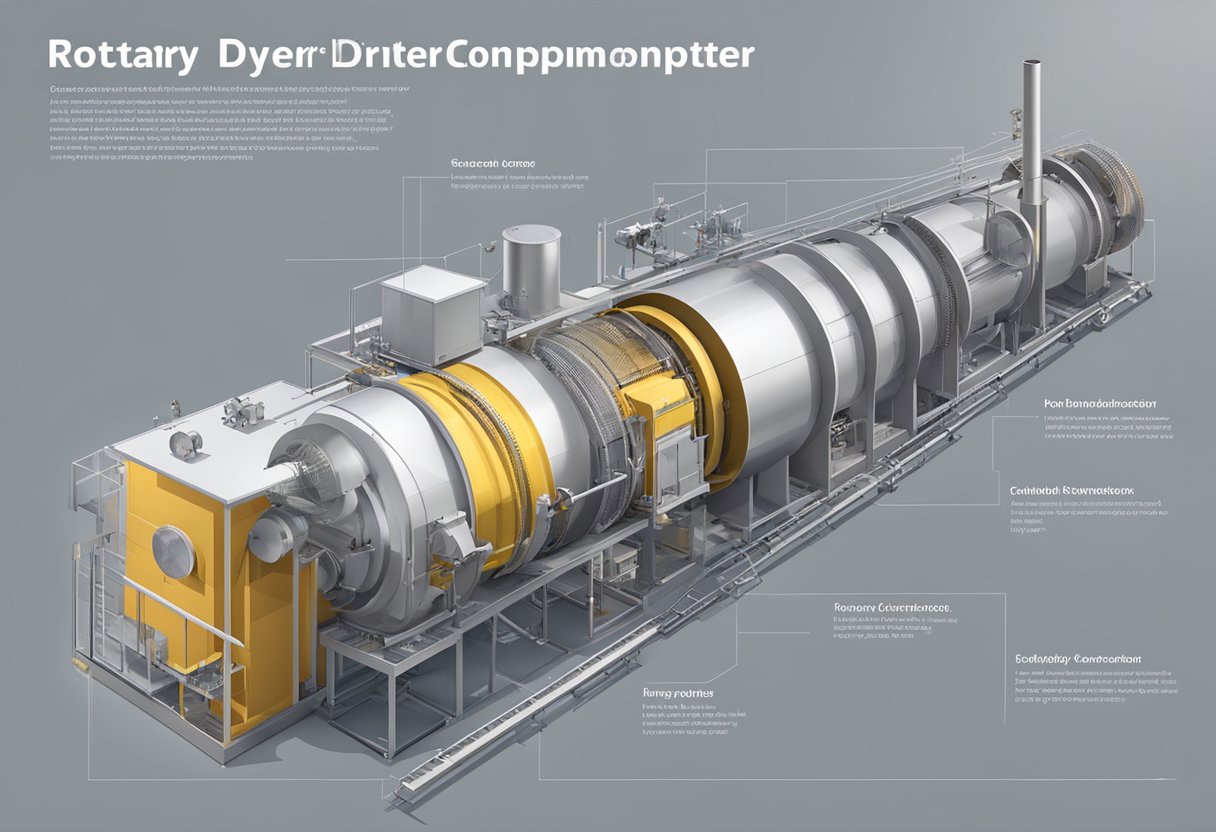
Shell Construction
The shell of a rotary dryer is typically made of carbon steel, stainless steel, or other high-temperature alloys. The shell is designed to withstand high temperatures and pressures, and is typically insulated to reduce heat loss. The thickness and diameter of the shell are determined by the required capacity and operating conditions of the dryer.
Flight Design
The flight design of a rotary dryer is critical to its operation and efficiency. The flights are the metal vanes that are welded to the inside of the shell and are responsible for lifting and cascading the material through the hot gas stream. The flight design must be carefully engineered to ensure that the material is evenly distributed and exposed to the hot gas stream for optimal drying.
Drive Assembly
The drive assembly of a rotary dryer is responsible for rotating the shell and driving the flights. The drive assembly typically consists of a motor, gearbox, and coupling. The motor is selected based on the required torque and speed, and the gearbox is selected based on the motor’s output and the required output speed and torque. The coupling connects the gearbox to the shell and allows for any misalignment between the two.
Sealing System
The sealing system of a rotary dryer is critical to its performance and efficiency. The sealing system is responsible for preventing air and gas leaks from the dryer, which can result in heat loss and reduced efficiency. The sealing system typically consists of a gland seal, which is located at the inlet and outlet of the dryer, and a lip seal, which is located at the drive end of the dryer. The sealing system must be designed to withstand the high temperatures and pressures of the dryer, and must be properly maintained to ensure optimal performance.
Material Considerations
When using a secador rotatorio, it is important to consider the material being processed. The following subsections highlight key material considerations for optimal performance.
Moisture Content
The moisture content of the material being processed is a critical factor to consider when using a secador rotatorio. The ideal moisture content varies depending on the type of material, but generally, a moisture content of 10-15% is recommended. If the material is too wet, it can cause issues with the drying process, such as uneven drying or clogging of the equipment. On the other hand, if the material is too dry, it can lead to dust generation and potential safety hazards.
Particle Size and Distribution
Particle size and distribution also play an important role in the performance of a secador rotatorio. The size and distribution of the material can affect the drying rate, heat transfer, and overall efficiency of the process. Ideally, the material should have a uniform particle size and distribution to ensure consistent drying. It is also important to consider the size and shape of the equipment, as larger particles may not fit or may cause blockages in the system.
In summary, when using a secador rotatorio, it is important to consider the moisture content and particle size and distribution of the material being processed to ensure optimal performance and efficiency.
Process Parameters
Temperature Control
The temperature control is a crucial process parameter in the operation of a rotary dryer. The temperature inside the dryer must be carefully monitored and controlled to ensure that the desired drying rate is achieved without damaging the product. The temperature is usually controlled by adjusting the hot gas temperature and the flow rate of the gas. The temperature range for most rotary dryers is between 200 to 300 °C.
Residence Time
Residence time is the amount of time that the material being dried spends inside the rotary dryer. It is an important process parameter that affects the quality of the final product. The residence time is determined by the length and diameter of the drum, the speed of rotation, and the angle of inclination. The residence time can be adjusted by changing the drum speed and the angle of inclination.
Rotation Speed
The rotation speed of the rotary dryer is another important process parameter that affects the drying rate and the quality of the final product. The speed of rotation is usually between 4 and 10 revolutions per minute (RPM), depending on the size of the drum and the material being dried. A higher rotation speed can increase the drying rate, but it can also cause the material to be damaged. Therefore, the rotation speed must be carefully controlled to achieve the desired drying rate without damaging the product.
In summary, the process parameters of temperature control, residence time, and rotation speed are crucial in the operation of a rotary dryer. These parameters must be carefully monitored and controlled to ensure that the desired drying rate is achieved without damaging the product.
Energy Efficiency and Performance
Heat Recovery Systems
Secador rotatorio is a highly efficient equipment that is designed to dry a wide range of materials. One of the key factors that contribute to its efficiency is the heat recovery system. This system is responsible for capturing the heat that is generated during the drying process and using it to preheat the incoming air. By doing so, the equipment can achieve significant energy savings, which translates into lower operating costs.
The heat recovery system works by using a heat exchanger to transfer the heat from the exhaust air to the incoming air. This process helps to increase the temperature of the incoming air, which reduces the amount of energy required to heat it to the desired level. As a result, the equipment can operate at a lower temperature, which reduces the risk of overheating and extends its lifespan.
Optimization Techniques
In addition to the heat recovery system, secador rotatorio also incorporates a range of optimization techniques to improve its performance. These techniques include:
- Variable speed drives: This feature allows the equipment to adjust its speed based on the load, which helps to reduce energy consumption and improve efficiency.
- Insulation: The equipment is designed with high-quality insulation materials to prevent heat loss and reduce energy consumption.
- Automatic controls: The equipment is equipped with sensors and controls that monitor the temperature, humidity, and other parameters to ensure optimal performance.
By incorporating these optimization techniques, secador rotatorio can achieve high levels of performance and efficiency, which makes it an ideal choice for industrial drying applications.
In conclusion, secador rotatorio is a highly efficient equipment that is designed to deliver superior performance while minimizing energy consumption. Its heat recovery system and optimization techniques make it an ideal choice for a wide range of industrial drying applications.
Maintenance and Safety
Routine Inspection
To ensure the optimal performance of the secador rotatorio, routine inspections are necessary. The inspection should include a thorough examination of all parts of the equipment, including the drum, bearings, seals, and drive components. Any signs of wear and tear, cracks, or other damages should be addressed immediately to prevent further damage or failure.
Preventive Maintenance
Preventive maintenance is crucial to extend the lifespan of the secador rotatorio. Regular cleaning, lubrication, and adjustments of the equipment are necessary to ensure its smooth operation. The cleaning should be performed with non-abrasive materials to avoid damaging the surface of the equipment. Lubrication should be done according to the manufacturer’s recommendations to prevent over-lubrication or under-lubrication.
Safety Protocols
Safety protocols must be followed at all times when working with the secador rotatorio. Operators should wear appropriate personal protective equipment (PPE), including gloves, safety glasses, and hearing protection. Before starting the equipment, ensure that all guards and safety devices are in place and functioning correctly. Never attempt to bypass or disable any safety devices.
In case of any malfunction or emergency, operators should be trained on how to shut down the secador rotatorio safely. A shutdown procedure should be in place and posted near the equipment for easy reference. Regular training and refresher courses should be provided to all operators to ensure they are aware of the safety protocols and procedures.
Overall, regular maintenance and adherence to safety protocols are essential to ensure the safe and efficient operation of the secador rotatorio.