
Small Screw Conveyor: A Compact Solution for Material Handling
Small Screw Conveyor: A Compact Solution for Material Handling
A small screw conveyor is a type of conveyor system that is designed to move materials from one point to another. It is commonly used in industrial settings, such as manufacturing plants and warehouses, to transport materials such as powders, grains, and other bulk materials. The conveyor consists of a rotating screw that moves the material along a trough or tube.
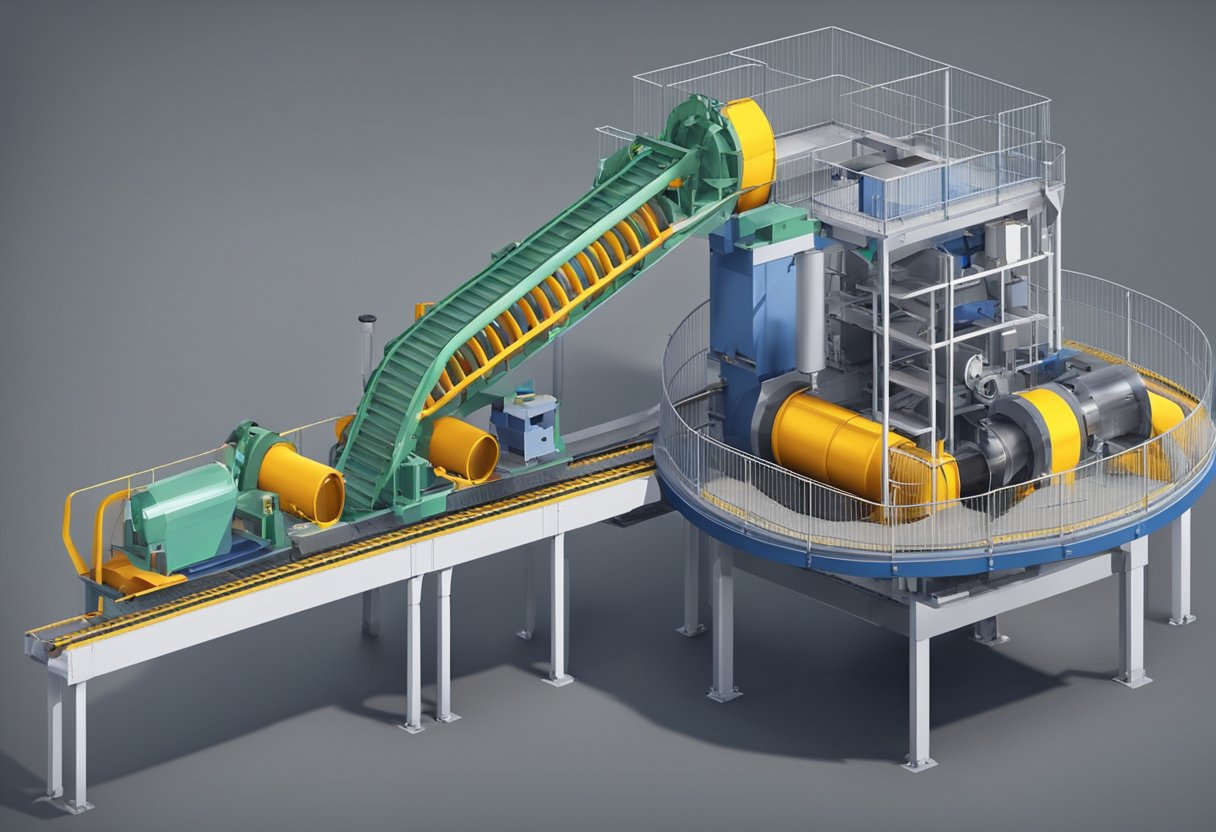
Small screw conveyors are ideal for transporting materials over short distances. They are compact and can be easily installed in tight spaces. They are also easy to maintain and operate, making them a popular choice for many industries. Some of the common applications of small screw conveyors include food processing, chemical processing, and mining.
Design Principles

Screw Design
The design of the screw is a critical factor in the performance of a small screw conveyor. The screw must be designed to provide maximum efficiency and reliability while minimizing wear and tear. The shape and size of the screw should be carefully considered to ensure that it can handle the specific material being conveyed.
In general, a small screw conveyor will have a helical screw that rotates inside a trough. The screw can be designed with varying pitch, diameter, and length to accommodate different materials and flow rates. The pitch of the screw determines the amount of material that is moved with each revolution, while the diameter and length of the screw affect the overall capacity of the conveyor.
Conveyor Capacity
The capacity of a small screw conveyor is determined by a variety of factors, including the size and shape of the screw, the speed of rotation, and the angle of incline. The capacity of the conveyor can be calculated using standard formulas based on the size and shape of the screw, as well as the material being conveyed.
It is important to ensure that the conveyor is not overloaded, as this can lead to excessive wear and tear on the equipment. Additionally, the speed of the conveyor should be carefully controlled to ensure that the material is moved at a consistent rate and that there is no buildup or blockage in the trough.
Incline and Flow Control
The angle of incline and the flow control of a small screw conveyor are important factors to consider when designing the system. The angle of incline will affect the capacity of the conveyor, as well as the speed and efficiency of the material flow.
Flow control mechanisms, such as gates, valves, or variable speed drives, can be used to regulate the flow of material through the conveyor. These mechanisms can help to prevent overloading and ensure that the material is moved at a consistent rate.
Overall, the design principles of a small screw conveyor are focused on maximizing efficiency and reliability while minimizing wear and tear. By carefully considering the design of the screw, the capacity of the conveyor, and the angle of incline and flow control, it is possible to create a system that is optimized for the specific material being conveyed.
Types of Small Screw Conveyors

Small screw conveyors are used to transport materials in various industries, such as food processing, agriculture, and mining. They come in different types, each with its own unique features and benefits. Here are three common types of small screw conveyors:
Shafted Screw Conveyors
Shafted screw conveyors are the most common type of screw conveyor. They consist of a rotating helical screw blade, also known as an auger, which is enclosed in a tube or trough. The auger is connected to a shaft that rotates to move the material along the length of the conveyor.
Shafted screw conveyors are ideal for handling dry to semi-fluid materials with low to moderate viscosity. They can be used for horizontal, inclined, or vertical transportation, depending on the application. They are also available in various sizes and configurations to suit different material handling needs.
Shaftless Screw Conveyors
Shaftless screw conveyors are similar to shafted screw conveyors, except that they do not have a central shaft. Instead, the auger is supported by a spiral-shaped steel wire, which is enclosed in a flexible tube or trough.
Shaftless screw conveyors are ideal for handling sticky, stringy, or fibrous materials that tend to wrap around a central shaft. They can also handle larger solids and have a higher capacity than shafted screw conveyors. They are commonly used in wastewater treatment plants, pulp and paper mills, and other industries.
Flexible Screw Conveyors
Flexible screw conveyors, also known as helix conveyors or spiral conveyors, are designed to transport materials in a flexible tube or casing. The auger is made of a flexible, spring-like material, which allows it to bend and flex around obstacles.
Flexible screw conveyors are ideal for handling powders, granules, and other free-flowing materials. They are easy to install, operate, and maintain, and can be used for horizontal, inclined, or vertical transportation. They are also available in various diameters and lengths to suit different material handling needs.
In conclusion, small screw conveyors are versatile and reliable equipment for transporting materials in various industries. By choosing the right type of screw conveyor for the application, operators can ensure efficient, safe, and cost-effective material handling operations.
Material Considerations

When selecting a small screw conveyor, it is important to consider the materials being handled. Different materials have different characteristics that can affect the performance and lifespan of the conveyor.
Abrasive Materials Handling
Abrasive materials can cause excessive wear and tear on the conveyor components, leading to increased maintenance and downtime. To minimize these issues, it is recommended to use abrasion-resistant materials for the conveyor components such as the screw, trough, and bearings.
Corrosive Materials Handling
Corrosive materials can cause damage to the conveyor components, leading to premature failure. To prevent this, it is important to use materials that are resistant to corrosion such as stainless steel or plastic. It is also recommended to use coatings or liners to protect the components from corrosion.
Food-Grade Applications
In food-grade applications, it is important to use materials that are safe for contact with food and can withstand cleaning and sanitization. Stainless steel is a common choice for food-grade applications due to its durability, corrosion resistance, and ease of cleaning. It is also important to consider the design of the conveyor to minimize areas where food particles can accumulate and potentially cause contamination.
Overall, selecting the appropriate materials for a small screw conveyor can improve its performance, reduce maintenance, and increase its lifespan.
Manufacturing Processes
Fabrication Techniques
Small screw conveyors are typically manufactured using various fabrication techniques such as welding, bending, and cutting. The fabrication process begins with cutting the raw materials such as steel or stainless steel sheets into the required length, width, and thickness. The cut pieces are then bent using specialized machines to create the required shape and form.
Welding is another crucial technique used in manufacturing small screw conveyors. The welding process involves joining two or more metal parts together using heat and pressure. This technique is used to create the body of the conveyor and to attach the screw to the body. The welding process used depends on the type of material being used and the application of the conveyor.
Material Finishing
Material finishing is an essential step in the manufacturing process of small screw conveyors. It involves applying a surface treatment to the metal to improve its appearance, durability, and resistance to corrosion. The most common finishing techniques include painting, powder coating, and galvanizing.
Painting is the process of applying a coat of paint to the metal surface of the conveyor. This technique is used to improve the appearance of the conveyor and to protect it from corrosion. Powder coating is a more durable finishing technique that involves applying a layer of dry powder to the metal surface and then curing it under high heat. This technique offers superior protection against corrosion and abrasion.
Galvanizing is a process that involves coating the metal surface of the conveyor with a layer of zinc. This technique provides excellent protection against corrosion and is commonly used in harsh environments. It also gives the conveyor a shiny and attractive appearance.
Operational Parameters
Speed and Efficiency
The speed and efficiency of a small screw conveyor are critical operational parameters that determine the productivity and throughput of the system. The speed of the conveyor is determined by the rotational speed of the screw, which can be adjusted to meet the specific requirements of the application. Increasing the speed of the screw can improve the throughput of the system, but it can also affect the efficiency and cause material degradation, which can result in increased maintenance requirements.
The efficiency of the conveyor is determined by the design of the screw and the material being conveyed. The pitch, diameter, and length of the screw can be customized to optimize the efficiency of the system. The material being conveyed can also affect the efficiency, as some materials may require a different screw design or speed to prevent material degradation.
Maintenance Requirements
Maintenance requirements are another critical operational parameter that must be considered when designing and operating a small screw conveyor. Regular maintenance is essential to ensure the system operates efficiently and reliably. The maintenance requirements of the conveyor depend on the specific design and application, but some common maintenance tasks include lubrication, inspection, and cleaning.
Lubrication is critical to ensure the screw and other components operate smoothly and prevent wear and tear. Regular inspections can help identify any potential issues before they become major problems. Cleaning is also essential to prevent material buildup and contamination, which can affect the efficiency and reliability of the system.
Overall, the speed and efficiency and maintenance requirements are critical operational parameters that must be carefully considered when designing and operating a small screw conveyor. By optimizing these parameters, it is possible to improve the productivity and reliability of the system, while minimizing maintenance requirements and downtime.
Installation Guidelines
Space Requirements
Before installing the small screw conveyor, it is important to ensure that enough space is available for the equipment. The conveyor should be installed in a location that provides sufficient clearance for maintenance and cleaning. The recommended clearance is at least 18 inches on all sides of the conveyor.
It is also important to consider the height of the conveyor. The height should be such that the operator can easily access the equipment for maintenance and cleaning. The recommended height is about 6 feet from the ground.
Mounting and Alignment
Mounting and alignment are crucial for the proper functioning of the small screw conveyor. The conveyor should be mounted on a sturdy foundation that can withstand the weight and vibration of the equipment.
Alignment is also important to ensure that the conveyor operates smoothly and efficiently. The conveyor should be aligned with the discharge and receiving equipment to avoid any spillage or blockage.
It is recommended to use a spirit level during installation to ensure that the conveyor is level. The conveyor should also be aligned horizontally and vertically to prevent any misalignment.
In conclusion, following these installation guidelines will help ensure the proper functioning of the small screw conveyor. Proper space requirements, mounting, and alignment are crucial for the efficient operation of the equipment.
Safety and Compliance
Safety Features
Small screw conveyors are designed with safety features to ensure that they are safe to operate. One of the most important safety features is the guard covering the rotating screw. This guard prevents operators from coming into contact with the screw, which could cause serious injury.
Another safety feature is the emergency stop button. This button is located in an easily accessible location and can be used to quickly stop the conveyor in case of an emergency. Additionally, small screw conveyors are equipped with safety switches that prevent the conveyor from operating if any of the safety guards are open or if there is a problem with the motor.
Regulatory Standards
Small screw conveyors must comply with various regulatory standards to ensure that they are safe and reliable. One of the most important standards is the ANSI/ASME B20.1 Safety Standard for Conveyors and Related Equipment. This standard outlines the safety requirements for conveyors and specifies the design, construction, installation, operation, and maintenance requirements for conveyors.
In addition to the ANSI/ASME B20.1 standard, small screw conveyors must also comply with OSHA regulations. OSHA requires that all machinery be properly guarded and maintained to prevent accidents and injuries. Small screw conveyors must also comply with other relevant standards, such as the National Electrical Code (NEC) and the International Building Code (IBC).
Overall, small screw conveyors are designed with safety in mind and must comply with various regulatory standards to ensure that they are safe and reliable. By following these standards and ensuring that the conveyor is properly maintained, operators can help prevent accidents and injuries in the workplace.
Troubleshooting
Common Issues
Small screw conveyors are widely used in various industries, but they can sometimes experience issues that affect their performance. Here are some common issues that may arise:
- Blockages: Blockages can occur when the material being conveyed is too large or has a tendency to clump together. This can cause the screw to jam, which can damage the conveyor or cause it to stop working altogether. To prevent blockages, it is important to ensure that the material being conveyed is the correct size and consistency for the conveyor.
- Wear and Tear: Over time, the screw and other components of the conveyor can become worn or damaged. This can cause the conveyor to malfunction or stop working altogether. Regular maintenance and inspection can help identify any issues before they become serious problems.
- Incorrect Installation: If the conveyor is not installed correctly, it may not function properly. This can cause issues such as vibration, noise, and reduced efficiency. It is important to follow the manufacturer’s instructions carefully when installing a small screw conveyor.
Problem-Solving Methods
If you encounter any issues with your small screw conveyor, there are several problem-solving methods that you can use:
- Identify the Problem: The first step in solving any issue is to identify the problem. This may involve inspecting the conveyor, checking for blockages, or testing the motor and other components.
- Consult the Manual: If you are unsure how to resolve an issue, consult the manufacturer’s manual for guidance. The manual may provide troubleshooting tips and instructions for resolving common issues.
- Perform Maintenance: Regular maintenance can help prevent issues from occurring in the first place. This may involve cleaning the conveyor, inspecting it for wear and tear, and replacing any damaged components.
By following these troubleshooting tips, you can help ensure that your small screw conveyor operates smoothly and efficiently.
Case Studies
Industry Applications
Small screw conveyors have a variety of industrial applications due to their ability to transport materials in a precise and controlled manner. One example of this is in the food industry, where small screw conveyors are used to transport ingredients such as sugar, flour, and spices from storage containers to mixing machines. This ensures that the correct amount of each ingredient is added to the mixture, resulting in consistent quality of the final product.
Another industry that benefits from small screw conveyors is the pharmaceutical industry. These conveyors are used to transport powders and granules, ensuring that the correct amount of each ingredient is added to the mixture. This is critical in pharmaceutical manufacturing, where precise dosages are required to ensure the safety and efficacy of the final product.
Performance Analysis
Small screw conveyors are designed to operate efficiently and reliably, even in harsh industrial environments. They are capable of transporting materials at a range of speeds and capacities, depending on the specific application.
One important factor to consider when selecting a small screw conveyor is the material being transported. Some materials may be abrasive or corrosive, which can cause wear and tear on the conveyor components over time. It is important to select a conveyor that is designed to handle the specific material being transported to ensure long-term reliability.
Another factor to consider is the required throughput. Small screw conveyors are capable of transporting materials at a range of speeds and capacities, depending on the specific application. It is important to select a conveyor that is capable of meeting the required throughput to ensure efficient operation.
Overall, small screw conveyors are a versatile and reliable solution for a variety of industrial applications. By selecting the right conveyor for the specific application, manufacturers can ensure consistent quality and efficiency in their operations.
Future Trends
Technological Innovations
As technology continues to advance, small screw conveyors are expected to become more efficient and effective. One of the most significant technological innovations in this field is the use of automation. With the help of automation, small screw conveyors can be programmed to operate with greater precision and accuracy, reducing the risk of errors and improving overall efficiency.
Another technological innovation that is expected to have a significant impact on the small screw conveyor industry is the use of sensors. By integrating sensors into the design of small screw conveyors, manufacturers can monitor the performance of the machines in real-time and make adjustments as needed. This can help to reduce downtime and improve the overall efficiency of the conveyor system.
Sustainability Considerations
As concerns about the environment continue to grow, sustainability considerations are becoming increasingly important in the design and manufacture of small screw conveyors. One of the most significant sustainability considerations in this field is the use of eco-friendly materials. By using materials that are biodegradable or recyclable, manufacturers can reduce their environmental impact and help to create a more sustainable future.
Another sustainability consideration is energy efficiency. By designing small screw conveyors that consume less energy, manufacturers can reduce their carbon footprint and help to conserve natural resources. This can be achieved through the use of efficient motors, as well as through the integration of energy-saving features such as variable speed drives.
Overall, the future of small screw conveyors looks bright, with technological innovations and sustainability considerations expected to drive the industry forward. With continued investment in research and development, small screw conveyors are likely to become even more efficient, effective, and sustainable in the years to come.