
The Challenges of Poultry Rendering in the Philippines Market
The Challenges of Poultry Rendering in the Philippines Market
Every time I start the rendering topic, I’d like to repeat what a rendering plant is. Because it’s not only a job or a work for me but also a small contribution to our mother earth. Rendering is a process that converts animal by-products, including those from poultry into valuable materials that are not intended for human consumption. Poultry by-products include feathers, blood, offal, and other waste materials from poultry processing plants. The primary goal is to transform poultry waste into useful products, reducing waste and promoting a more sustainable and circular economy. So a rendering plant can be a feathers rendering plant, a poultry waste rendering plant, a meat and bone rendering plant, a blood rendering plant, a fish rendering plant, a chicken rendering plant, a beef rendering plant, even a fat rendering plant, etc,.
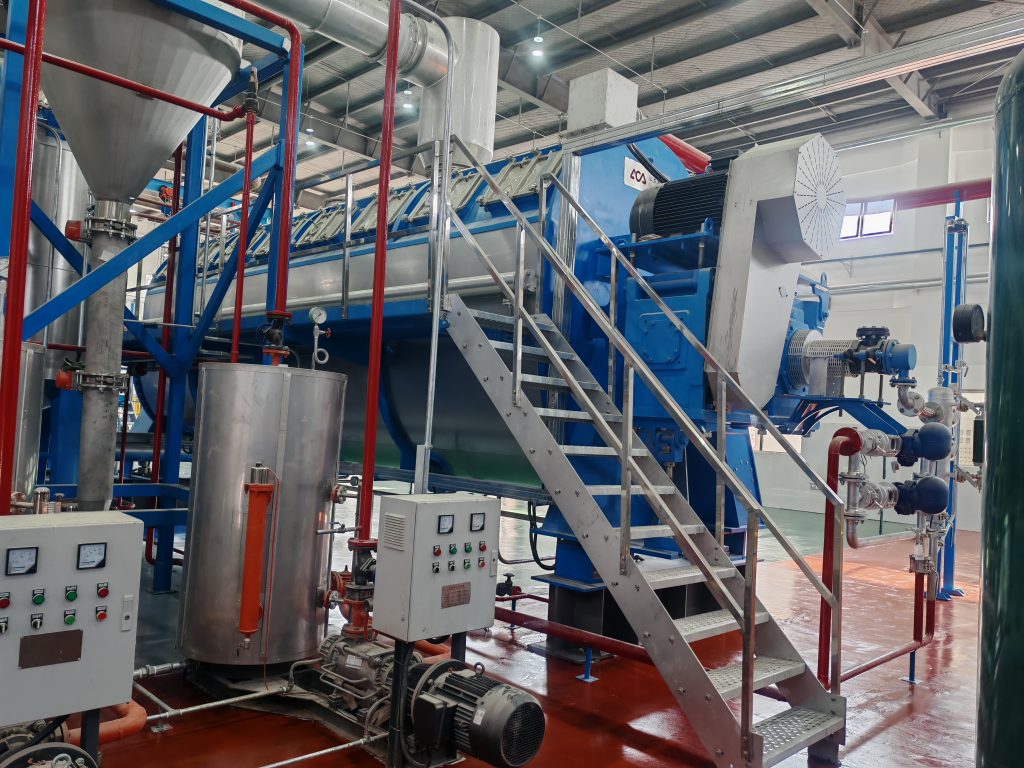
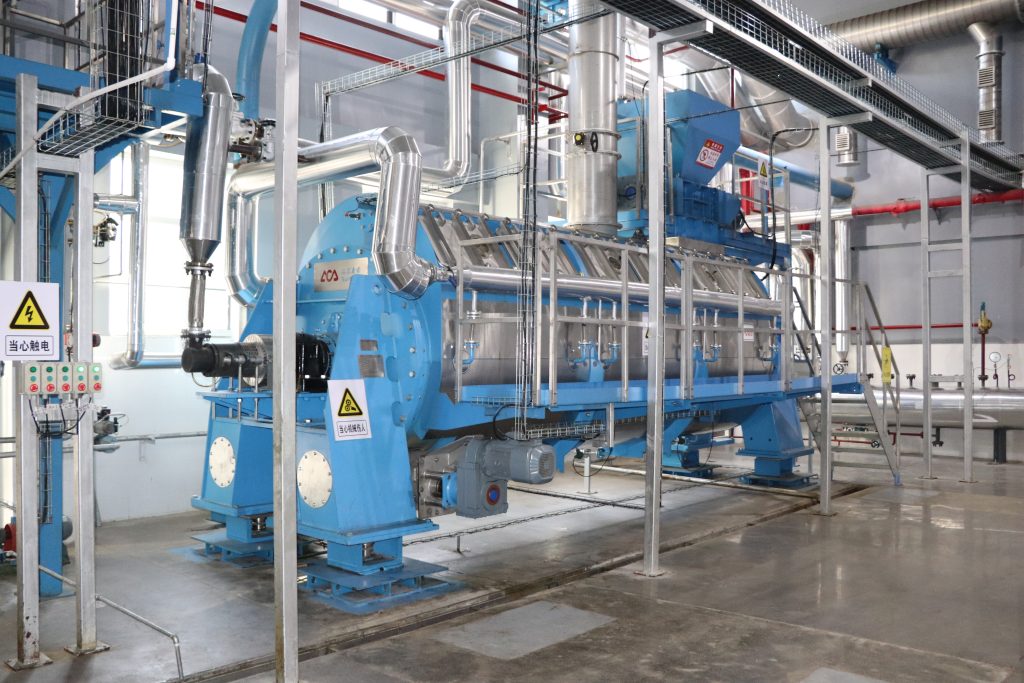
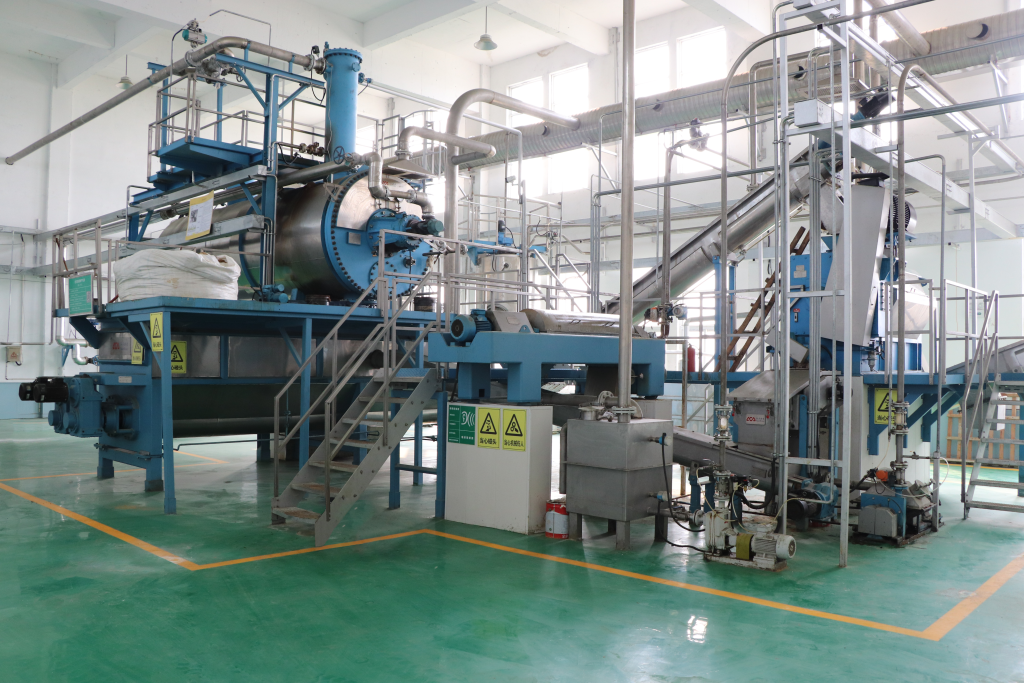
In the Philippines, the most is the feathers rendering plant. The general process is to use screw conveyors to load the wet feathers into the batch cooker. After hydrolysis and drying, discharge the finished products(feather meal) into a storage silo, then cool inside the storage silo. After the temperature reach less than 30℃,deliver the feather meal to a vibrating screen or a sifter. The equipment list is very simple. It doesn’t have material receiving bin, feather press, continuous cooker, disc dryer,meal cooler.
Why like this? It’s because the Philippines geographical characteristics. The Philippines has a lot of islands. The biggest one is Luzon. Transportation between islands is not as efficient as transportation between land and land. This also leads to the scale of the chicken slaughterhouse on each island will not be very large, which in turn means that the scale of the rendering plant will not be very large.
There are some disadvantages for these small rendering plants. The first one is the small rendering plant will cause the investors get back their investment in a late time. Small rendering plants have lower daily output. The second is the small rendering plant makes the investors have no budget to put up advanced odor control system. This led to an increase in complaints from neighbors. The third is the small rendering plant produce low quality feather meal. The materials stay inside the pressure tank longer time. It will cause feather meal parameters decreased.
How to solve it? First, build the database, summarize the size and quantity of the poultry dressing plants and slaughter houses. Second, try to contact each plant to show them the plan to build a rendering center in each island so that all the poultry dressing plants can deliver the feathers to this rendering center. Third, recommend Sunrise high-tech advanced equipment to the rendering center. Jiangsu Sunrise Environmental Protection Technology Co. Ltd has the continuous cooker and disc dryer which can less the processing time, improve production efficiency, reduce the costs and help customers maximize their profit margins. Sunrise Regenerative Thermal Oxidizer can help clients less minimum 98% odor. If no odor, no complaint from neighbour. That can keep the rendering plant alive for a long time.